Metal Core PCB factory in China
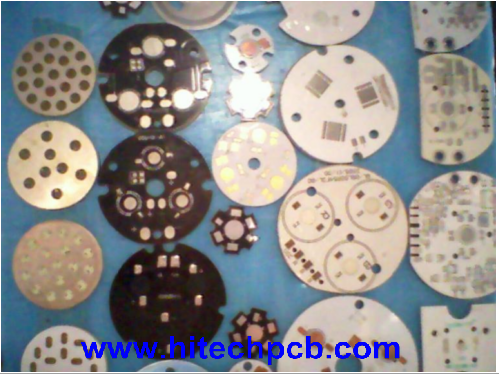
Wiith the growing popularity of light-emitting diode or LED technology, metal core PCBs or MCPCBs are being deployed to deal with the increased heat LEDs generate. Fig. 1 below shows a metal core PCB
.
Today, metal core PCBs are finding greater numbers of applications in the automobile industry, traffic light signal technology, in commercial buildings, shopping malls, and even inside homes.
MCPCBs use either an aluminum or copper core with the bottom side of the board serving as the heat sink. MCPCBs are also used to dissipate heat in intense power-generating analog circuitry.
Metal core PCBs are connected through mounting holes and screws through a box build’s chassis. In this arrangement, heat is not only dissipated through the metal core, but it is also transmitted to the chassis. Hence, an LED or analog device-populated board has a considerably larger surface finish for the purpose of dissipating that heat.
But here’s a word of caution about using MCPCBs – actually two things to be cautious about. One, you need to know that making an MCPCB is complex and complicated because a metal layer is laminated with FR4, a glass-base material. Therefore, the chemistry for lamination is different during board fabrication. There is a fair possibility that there would be voids underneath the lamination, if it is not bonded properly. Two, a fixture to dissipate the heat from the metal core needs to be carefully defined and designed. Both these concerns demand experience.
At Hitechpcb, we’ve been doing this for a long time, and can successfully guide you through your next MCPCB project. We have worked with over half a dozen LED PCB manufacturers over 15 years and have seen enormous amounts of different applications using MCPCBs.